PSHE
Plate shell heat exchanger is a new type of plate heat exchanger that combines
Classification:
Plate shell heat exchanger
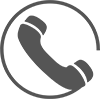
Hotline:
PSHE
Product Introduction
Plate shell heat exchanger is a new type of plate heat exchanger that combines the characteristics of tube shell and plate heat exchangers. It has the advantages of high heat transfer efficiency and compact structure of plate heat exchangers, as well as the suitability of tube shell heat exchangers for high temperature and high pressure working conditions. It is an advanced and efficient energy-saving heat exchanger, mainly used in industries such as petrochemicals.
The plate shell heat exchanger consists of two parts: the pressure vessel shell and the heat transfer plate bundle. The plate bundles welded together in parallel are longitudinally installed inside the shell. The shell of a pressure vessel is subjected to fluid pressure, and the plate bundle is composed of several plates welded together. The flow channels of the plates are in a herringbone corrugated shape, and adjacent plates are inverted. The corrugated contact between the plates forms a contact point. These contacts help to keep the fluid in a turbulent flow state throughout the entire heat transfer process, which can improve heat transfer efficiency while suppressing the generation of dirt on the plate surface. The plate bundle is assembled by welding plates, fixed on the bracket inside the pressure vessel shell, and connected to the shell through a corrugated expansion joint. The plate bundle is easy to disassemble.
Construction and working principle
The plate and shell heat exchanger can be divided into two major parts: plate tube bundle and shell. The plate bundle is equivalent to the tube and shell tube bundle. Each plate bundle element is a pair of two cold pressed (or explosively formed) metal Flat noodles welded together closely at the contact, forming a plate tube with multiple flat flow channels. In a heat exchanger, these flat plate tube channels form the plate side of the plate shell heat exchanger, equivalent to the tube side of the tube shell heat exchanger, and each plate bundle element is equivalent to a tube. Many board tubes of varying widths are arranged in a certain order. To maintain the spacing between the plate tubes, metal strips are inserted at both ends of adjacent plate tubes and welded together with the plate tubes. The two ends of the plate tube form a tube plate, thereby firmly connecting many plate tubes together to form a plate bundle. The end face of the plate bundle presents several flat flow channels. The spacing between the boards in the middle of the bundle is maintained by the protrusions on the bundle components. The plate bundle is assembled inside the shell, and the longitudinal expansion difference is eliminated by sliding sealing between it and the shell. The equipment section is generally circular, but there are also rectangles, hexagons, etc.
Product Technical Features
1. High heat transfer efficiency. Corrugated plates have the function of "static stirring", which makes fluid flow prone to turbulence, and the fluid velocity distribution is uniform, enabling "pure counterflow". Both sides of the heat transfer wall have high surface heat transfer coefficients.
2. Not easy to scale, easy to maintain and clean.
3. Small temperature difference and high heat utilization efficiency. The temperature difference between the cold and hot ends of the plate and shell heat exchanger is small, which can recover more heat and save operating costs of the device.
4. Compact structure and light weight. The heat transfer area per unit volume of a plate and shell heat exchanger can increase by 70% compared to a tube and shell heat exchanger.
5. High welding technology requirements.
Previous:
None
Next:
Related Products
Related Products
Messages
Your voice is crucial here. Whether you have valuable suggestions for our products and services, encounter questions that need to be answered, or want to share your usage experience, we are always willing to listen.